Why did agriculture mechanize and not construction?
constructionphysics.substack.com · by Brian PotterOn her YouTube channel, Belinda Carr poses an interesting question: why did agriculture mechanize (ie: replace manual labor with machine labor), but not construction?
Construction is often contrasted with factory-based production, but in many ways agriculture is a better comparison. Both construction and agriculture have traditionally been labor intensive activities. Both take place outdoors, exposed to the elements. And both require the work to be spread over a large, unstructured environment (unlike factory production, where the entire process can be tightly controlled).
But unlike construction, agriculture has seen massive drops in labor required to perform it. The percentage of the population employed in agriculture has declined from 40 to 60% in 1700, to less than 2% today. Between 1900 and 2015, the number of people employed in agriculture in the US declined from 12 million to 2 million, a period in which US farm output (as well as total population) quadrupled:
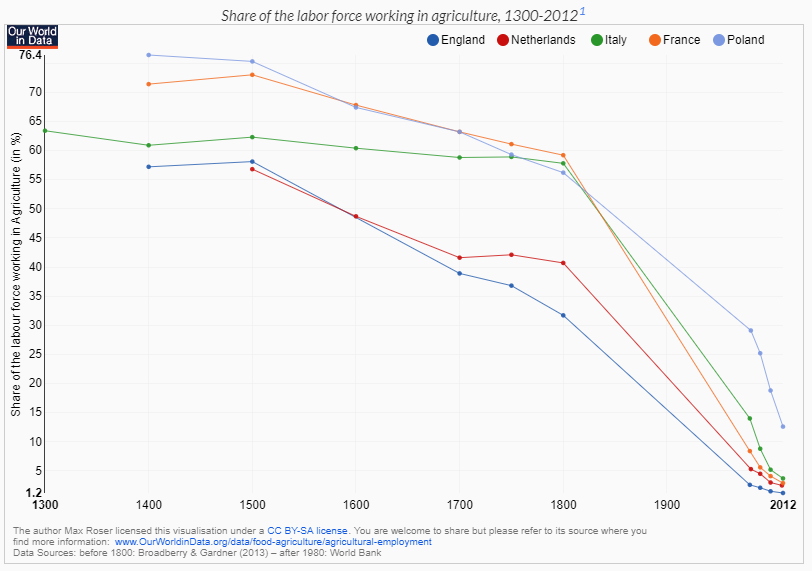
Much of this reduction in labor was relatively recent. From 1940 to 1960 alone, Richard Day estimates that the labor required per bushel of cotton was reduced by 90%. The introduction of the tomato harvester reduced the labor required to harvest tomatoes by 50% between 1965 and 1973:
Construction labor productivity, on the other hand, has consistently lagged behind. Between 1964 and 2012, Paul Teicholz estimates that construction labor productivity actually decreased slightly, by about 0.32% per year. Over the same time period agriculture labor productivity more than quadrupled.
The technology that has improved agriculture is extremely wide ranging, but a significant fraction of this gain is due to mechanization. Over the past 100 years the number of machines on farms has dramatically increased:
Agriculture doesn’t necessarily seem like an obvious candidate for mechanization. A field of crops contains thousands of individual plants, no two of which are exactly alike. Unlike factory produced products, which can be effectively identical, each individual fruit [0] will have a slightly different size, shape, location, etc. Labor-based harvesting involves stringing together a series of movements that are simple for a human to perform (reach out, pick the fruit, put it in the basket), but have proved to be fiendishly complicated to mimic with a machine, and which will be different for every crop. And while there are some degrees of freedom in adapting crops for harvestability, they can’t be designed from scratch around the process the same way products can be in manufacturing.
Given all these difficulties, how was agriculture able to be mechanized so effectively?
Mechanization
The process of mechanization is taking some human-performed task, decomposing it into a series of movements, and then constructing a machine to capture those movements. Once the movement is freed from the physical limits of a human body, it can be improved - operating at a larger scale or a faster rate than a human could perform it. For instance, prior to 1840 wheat was harvested by manually swinging a grain cradle (a modification of the scythe to keep the grain stems aligned). Cyrus McCormick’s mechanical reaper captured the motion of swinging the scythe with a rotating mechanism attached to a series of blades, which could then be pulled by a horse:
Mechanization doesn’t require replicating a human’s movement exactly. The greatest gains from mechanization occur when a complex human movement can be replaced with a simple mechanical movement. A ship’s propeller doesn’t move the same way a fish’s tail fin does - it replaces the back and forth movement of the tail with a simple rotation that yields a similar result.
Mechanization has traditionally required repetitive movements that can be performed over and over again unchanged. Partly this is due to the increase in size and complexity that results in adding more movements - each additional movement requires an additional mechanism to capture it. But it’s also in large part an information problem - if a machine is capable of multiple possible movements, it needs a way to "decide" which one to pick, which requires it to know something about the state of the surrounding environment and it’s position in it. A robot arm is capable of a wide array of possible movements, and isn’t necessarily complicated mechanically (a series of motors and gearboxes attached via lever arms). Early robot arms first appeared in the 1930s. But the first practical robot arm had to wait until information processing and control technology had caught up. The less repetitive the task, and the more dependent it is on environmental context, the less successful mechanization has been.
Agriculture and Mechanization
Agriculture has seen amazing labor productivity gains in part because, despite appearances, it is unusually amenable to being decomposed into repetitive tasks.
A crop being harvested is subject to a great deal of variation - individual fruits will vary in size, shape, color, location on the plant, force required to separate them from the plant, etc. But the fruits themselves have some physical property or properties that reliably differentiate them from their surroundings - they are firmer, larger, have different shape, different weight, different density, and so on. Crop harvesting machines work via mechanisms that in essence, act as filters - they use these physical differences to separate the fruit from the rest of the plant and/or soil.
An ear of corn, for instance, is wider than the stalk it attaches to. Corn harvesters work by forcing the stalk to pass through an opening that’s too narrow for the ear of corn. As the combine passes over the cornstalk, the ear of corn pops off, after which it makes its way through the rest of the combine.
Other harvesting equipment works in a similar way. Potato harvesters work by scooping up the ground the potatoes are planted in, then running it over a grate which separates the dirt and debris from the potatoes. Carrot harvesters work by pulling the entire row of plants up, then running a blade below where the carrot starts. Olive harvesters work by physically shaking the trees enough so that the olives separate from the tree and can be collected.
A crop harvesting machine can thus ignore almost all the specific information that a human would use to harvest a plant. It doesn’t need to know exactly where the ear of corn is [1], or how big it is, or how firmly it’s attached to the stalk. The machine just needs to have a few pieces of critical information about the crop it’s harvesting built into the mechanism, that are sufficient to only let the fruit pass through (to some degree of probability). The cotton gin, for instance, worked by pulling the cotton fibers through a fine mesh that cotton seeds couldn’t pass through, eliminating the laborious work of removing them by hand.
Once an effective filtering mechanism is found, it’s just a matter of feeding as much input material (plants with unpicked fruit) into it as possible. This part is straightforward - the typical US farm is over 400 acres (made up of multiple 80 acre plots), and each acre will have thousands of individual plants. Typical corn farm density, for instance, is over 30,000 plants per acre, or over a million plants spread over 400 acres, all of which can be harvested with the same machine [2].
Crop harvesting, in essence, is a statistical process. It’s powered by the lack of overlap in the probability distributions of the physical traits of different parts of a plant.
Crops that can’t be harvested in this way remain extremely labor intensive and expensive to produce. Strawberries, for instance, must be picked by hand due to their fragile nature [3]. As a result, strawberries upwards of $2.00 per pound, and labor makes up about 40-60% of their production cost. For comparison, corn (which is harvested mechanically) costs somewhere in the neighborhood of 11 cents per pound, and labor consists of just over 1% of its production costs.
Timber harvesting provides an interesting example as well. Trees are harvested mechanically, but NOT via simple repetitive movements or a filter-like process. Instead, large boom-mounted saws cut down trees one at a time, using human-like movements (reach out, grasp tree, engage saw, move tree to truck). Thus despite being mechanized, timber harvesting doesn’t seem to have seen the same gains in labor productivity that other parts of agriculture have - between 1950 and 1980, rather than decreasing, Oregon’s logging employment moved more or less in concert with it’s volume of wood harvested.
Information, Manufacturing, and Construction
Manufacturing can’t operate on a filtering-based process that can be implemented via simple mechanisms. Building something involves putting a series of specific parts in specific places in a specific order. This is much harder to mechanize - at minimum it requires a separate movement (or series of movements) for each step in the process. And it almost always requires a large number of humans in place to handle movements that are too complex to mechanize (such as installing screws). Interestingly, this means manufacturing has been slower to mechanize than agriculture. Car manufacturing employment, for instance, nearly doubled in the US between 1940 and 1970, whereas in agriculture it dropped by more than half over the same period [4].
Construction has it even harder than manufacturing does. Construction has the same issues with part placement and sequencing, and on top of that must cope with an uncontrolled, non-repetitive environment. A manufacturing process, once in place, can be repeated thousands or millions of times. But it’s very difficult to decompose a building in such a way that it can be produced by a sequence of repetitive movements, and it’s difficult to mass produce large numbers of identical buildings. With building construction, you’re putting specific parts in specific places, but you’re doing it in a different way every single time. The mechanization we do see exists at a very low level, with power tools for certain repetitive tasks such as nailing, sawing, and drilling, or with the production of individual building components [5].
Even the initial mechanization step of "decomposing the task into a series of movements" becomes difficult when you’re dealing with an object as large as a building. Manufacturing and agricultural machines need to be physically large enough to access and manipulate whatever object they’re working with, whether it’s an ear of corn or a Nissan Sentra. But a machine capable of manipulating every part of a building would be enormous, and seemingly just push the problem back a level (it would be so large that it would need to be assembled on-site, forcing you to build the machine before you could build the building). This is a problem that 3D gantry printers will have to figure out.
However, there are some areas of construction that don’t have these difficulties. Highway construction, for instance, is done with a process that isn’t unlike agriculture. It’s extremely repetitive (a section of road might extend for miles and miles), it’s built using large machinery capable of manipulating the individual components, and it uses components like gravel and asphalt that can be placed statistically (it doesn’t matter where an individual piece of aggregate goes). And we see that road construction, at least for a while, saw large labor productivity improvements (though the data here isn’t great):
The Future
One trend to keep an eye on is that we’re likely nearing the end of requiring repetitive, unchanging movements for efficient production processes.
Nonrepetitive movements are fundamentally an information problem - they require some method of telling a machine the state of the surrounding environment, and what to do depending on what that state is.
As software gets better and better, and as technologies like computer vision continue to improve, our ability to solve these information problems increases. Technologies like CNC milling, 3D printing, laser/plasma cutting, and even some steel sheet folding are already capable of quickly and cheaply fabricating different parts, one right after the other.
It’s possible we’ll start to see improvements in the area of robotic arms as well, which could have enormous effects on the construction industry. A robotic arm, paired with high end computer vision (or other feedback system), paired with some sort of tool-changer, would be a device theoretically capable of, say, performing a large fraction on-site construction tasks. It’s possible we’re on the cusp of some substantial industry changes as a result.
[0] - By fruit, I mean the crop that’s being harvested, as separate from the plant itself
[1] - Harvesters do often need to be aligned with the plants they’re harvesting, but not the individual fruits.
[2] - This repetitiveness also applies to other parts of the process, such as planting, or spraying. It’s the harvesting that prima facie seems more difficult to mechanize.
On the other hand, a 100,000 square foot building might have 30,000 wall studs in it, 5000 trusses, 12,000 sheets of drywall, 35,000 shingles, and many other components. In a sense the difficulty of mechanizing construction can be likened to the difficulty of replacing a 400 acre farm that contained a single crop with a 1 acre farm that contained 400 different crops.
[3] - Though efforts to develop a mechanical strawberry harvester date back to the 60s.
[4] - This is confounded somewhat by the fact that food is a necessity, and thus the market started out larger than it did for cars - but not as much as you might think. Both agricultural and motor vehicle output in the US increased substantially during the period in question (though motor vehicle output increased more).
[5] - Interestingly, we don’t even see mechanization in parts of construction that seem like it should obviously be possible. Masonry/bricklaying is an example. Building a masonry wall involves putting down thousands of identical masonry units, with identical movements - a seemingly perfect candidate for mechanization. And though mechanical masonry machines have existed as far back as 1967, they’ve failed to catch on - masonry remains a completely manual task.